Automated visual inspection refers to the use of advanced technology, such as cameras, sensors, and artificial intelligence (AI), to examine products and processes for defects, inconsistencies, or compliance with specifications. This system automates the task traditionally performed by human operators, ensuring consistent quality control while reducing errors.
The automated visual inspection system operates by capturing images of products and analyzing them against predetermined standards. By leveraging technologies such as machine learning and computer vision, these systems detect even the smallest deviations with incredible precision.
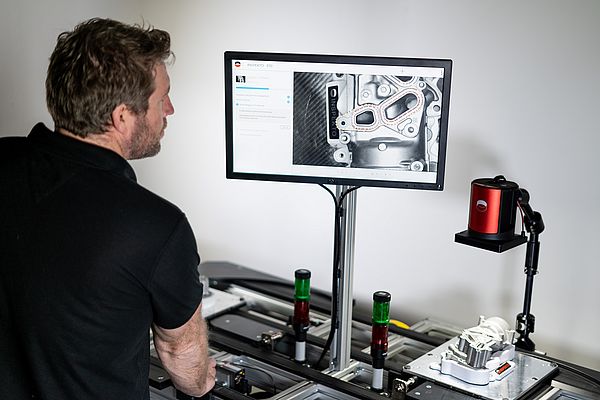
Applications in Industry
Automated visual inspection systems are widely used across industries, including automotive, electronics, pharmaceuticals, and food processing. For instance, in automotive automation, these systems inspect critical components like gears and engine parts to ensure safety and reliability. In semiconductor process automation, they verify the integrity of delicate microchips, where even microscopic defects can lead to product failures.
Companies like Siemens and Inspekto are at the forefront of delivering cutting-edge solutions like the Inspekto S70, designed for rapid deployment and high flexibility. Learn more about the capabilities of these systems on platforms such as Inspekto.
How Automated Visual Inspection Is Transforming Production Standards
Automated vision inspection systems are redefining production standards by minimizing human error and increasing operational efficiency. By integrating AI algorithms and real-time data analysis, these systems enhance quality control, ensuring compliance with stringent industry standards.
For example, Industry 4.0 initiatives emphasize the importance of intelligent manufacturing. Automated visual inspection systems align with these principles, enabling seamless integration with smart factories. Learn how Industry 4.0 impacts industrial automation and visual inspection technologies.
Enhancing Accuracy in Quality Control
The precision of automated visual inspection systems ensures that every product leaving the production line meets exact specifications. By using high-resolution cameras and sophisticated AI algorithms, these systems detect defects invisible to the human eye.
Key visual inspection factors influencing accuracy include lighting conditions, camera resolution, and the type of defects being analyzed. These systems adapt to different production environments, making them indispensable in sectors requiring rigorous quality control.
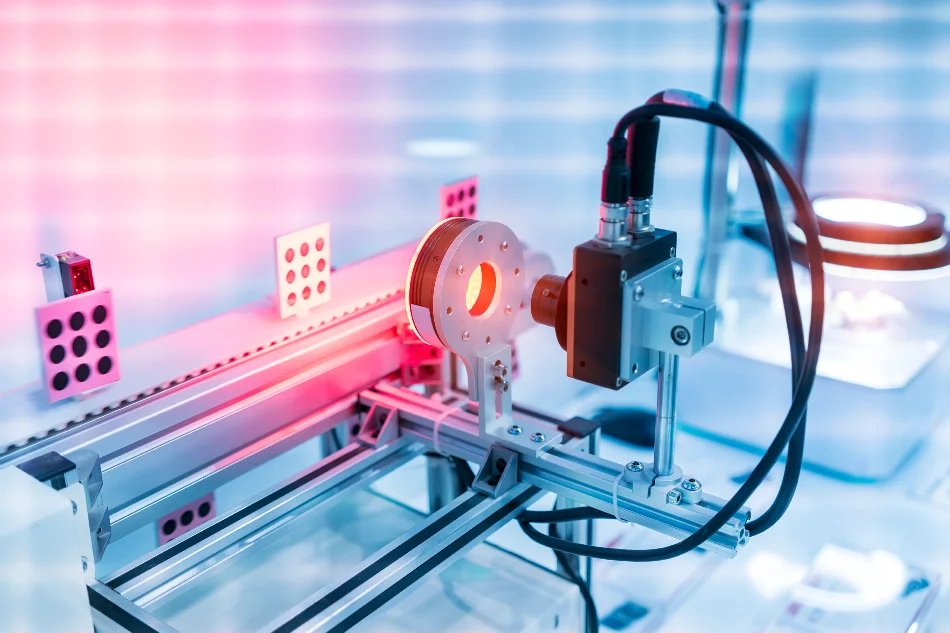
From AI to Algorithms: How Automated Visual Inspection Works and Why It Matters
How do vision inspection systems work? The process begins with image acquisition, where cameras capture detailed images of the product. These images are processed using machine learning algorithms trained to identify defects, anomalies, or specific features.
A basic principle of visual inspection involves comparing captured images against predefined standards. AI enhances this process by learning from vast datasets, enabling the system to identify complex patterns and make decisions with minimal human intervention.
Understanding visual inspection principles is crucial to leveraging its full potential. Explore how systems like Humphrey Automation integrate advanced inspection techniques to improve production efficiency.
Boosting Efficiency with Automated Visual Inspection
Efficiency is a cornerstone of automated visual inspection systems. By streamlining production workflows and reducing downtime, these systems significantly enhance throughput. Real-time monitoring capabilities ensure immediate detection and correction of defects, preventing costly production delays.
Incorporating automated visual inspection into custom engineering solutions allows businesses to tailor the system to their specific needs. Discover how custom solutions drive efficiency in various industries.
Various Types of Visual Inspection Techniques
There are several visual inspection types used in automated systems, each suited to specific applications:
- Surface Inspection: Identifies scratches, dents, or surface irregularities.
- Dimensional Inspection: Ensures components meet size and shape specifications.
- Assembly Verification: Confirms that parts are correctly assembled.
- Defect Detection: Detects cracks, chips, or other defects.
These techniques can be customized to meet the demands of industries such as automotive automation and semiconductor process automation.
Benefits of Automated Visual Inspection in Industrial Processes
The benefits of automated visual inspection systems are extensive:
- Increased Accuracy: Minimizes human error and detects minute defects.
- Enhanced Productivity: Reduces inspection time and increases throughput.
- Cost Savings: Lowers operational costs by preventing defective products from reaching customers.
- Scalability: Adapts to different production volumes and complexities.
Statistics show that automated systems can reduce inspection errors by up to 90% (Source: McKinsey & Company). Explore how these advantages align with the goals of custom engineering solutions.
Conclusion
Automated visual inspection systems represent a significant leap forward in quality control and production efficiency. By integrating advanced technologies like AI and machine learning, these systems ensure unparalleled accuracy and reliability across industries. From understanding visual inspection principles to exploring diverse applications, the potential of automated visual inspection is limitless.
As industries continue to embrace smart manufacturing, systems like the Siemens Inspekto S70 will play a pivotal role in shaping the future of automation. For businesses seeking to stay ahead of the curve, investing in automated visual inspection technologies is not just an option but a necessity.